
This issue is still available! Click here.
By Dave McCracken
“It takes a huge amount of streambed in motion to cause large portions of the river to form new high-grade deposits.”
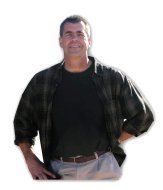
It only takes a small amount of water force to move sand-sized particles downstream in a riverbed. It takes more water force to move pea-sized gravel downriver, and even more force to move baseball-sized rocks, and so on. It also takes a greater amount of water force to move larger particles of gold, than it does to move smaller ones – just like other streambed materials.
There is a massive amount of gold in gold-bearing waterways which is so small in particle-size that it floats in a state of suspension in the river-water itself. Some amount of gold is moving downstream in any gold-bearing river at any given time. An increase in water-flow increases the amount of streambed material and gold that is moved downstream.
Normal winter storms, for the most part, can move large amounts of fine and ultra-fine gold down the gold-bearing rivers. But this gold is likely to be so widely dispersed throughout the overall river that it is of little value to the modern river-prospector.
Today’s modern river-prospector is mostly interested in that gold which lies inside and underneath naturally-formed streambeds. For the most part, this gold will remain locked in place until a storm of major proportions comes along. Such a storm can cause so much water force in the river that large sections of pre-existing streambeds, and the gold that is within them, are swept up and washed downstream.
When a storm or snow-runoff of huge dimensions comes along and creates so much force of water flow that large portions of the riverbed are torn up and washed down along the bedrock, large portions of the bedrock will also get pounded loose, and any gold which was trapped in that bedrock will become washed further downstream along with the rest of the streambed material.
“Rough bedrock makes the best gold traps.”
The amount of gold still sitting inside streambeds of proven gold-bearing rivers is incalculable; there is a whole lot of it! Much was left behind in low-grade deposits which the early miners were not capable of mining at a profit. While there may been a lot of gold in some sections of river during the gold-rush years, it might also have been too widely dispersed or sitting underneath too much overburden to make the gold worth mining in those days. Other very rich deposits were missed because they were out of sight. Without processing every bit of streambed (which they did not have the capability to do), the old-timers simply could not find all of the gold deposits that existed during their time. A lot of gold that was excavated was never recovered. It was washed out of the high streambed deposits, through sluice boxes, and right back into the present rivers and creeks. This was particularly true of hydraulic mining, where an estimated 59% of the gold was missed by many of the large and small operations alike.
Also, the last 150 years of erosion has washed more gold into the present rivers and streams out of higher and older streambeds, and out of some lodes that are still in existence.
In taking all of this into consideration, we are talking about a lot of gold still existing in these gold-bearing rivers. In some cases, there is more gold present now than the amount that has already been mined out of them.
When a major storm occurs in a gold-bearing area and tears up large portions of streambed, a great deal of gold is set free and put into motion downriver. A fair amount of this newly-released gold, because of its superior weight, will be deposited in common areas along the riverbed. This is the type of gold that the modern gold prospector should be sampling for. The same major storm which causes enough force to tear up large portions of streambed material will also deposit most of that material into newly formed natural streambeds-even in those same areas which were once mined by the early miners.
During full flood stage, when streambed material and gold are moving free in the waterway, because it is so heavy, most of the gold will travel along a rather narrow path. This path is often referred to as the “gold line” by prospectors. Almost all high-grade pay-streaks will be located along this specific path. Therefore, the first step in prospecting is to locate where the common gold path is within the waterway. This very important principle is demonstrated by the following two video segments. Please take careful note of how the gold is attracted to the common line in the simulated river, regardless of where it is fed into the waterway:
For the most part, normal winter storms occurring in gold country do not create enough water force to do this. A winter storm might be enough to sweep up small portions of streambed in faster-moving sections of river and redeposit new streambeds in those areas, but this small amount of movement is not likely to put paying quantities of gold into play in the riverbed. It takes a huge amount of streambed in motion to place substantial amounts of gold into movement. This causes large portions of the river to form new placer deposits. Such storms occur occasionally, and are the main cause for a streambed cutting deeper into the earth as time goes along. Most gold-bearing areas have had at least one of these major storms since the early 1960’s. Alaska has major storms along with massive snow runoffs. So flood forces like this happen more often there.
When millions and millions of tons of rocks, cobbles, and boulders are being swept downstream along the bedrock foundation during a huge storm, the ground shakes and vibrates, and the river rumbles like a huge loaded freight train. After a major storm has been through an area, the plant growth, underbrush and weeds which normally grow along the river gravel bars, will be washed away. This will also be true with a lot of the growth, including trees, along the riverbanks.
It takes an incredible amount of water force to cause an entire riverbed to move downstream, but this is what it takes to form many new placer deposits in the river.
The following video was taken during the major flood storm that took place along the Klamath River in Northern California during early 1997. If you watch the footage closely, you will see places where the river is flowing down river with the full force of the storm, and you will see other places right alongside where the water is flowing in a reverse direction. This is important! Take note of the incredible amount of boiling which takes place between the different directions of flow. These are pay-streaks in the making; places within the waterway at flood stage where the river is not really flowing in either direction; but rather is boiling like a kettle of superheated water between opposing forces. Gold concentrates within these areas because there is not enough water velocity to keep it moving along. Each place along the common gold line within the waterway that a boil like this is created by the interplay of reverse-flows is where a prospector will find the high-grade pay-streaks. See how big the boiling areas are?
The earlier idea that gold drops into the river and simply is vibrated down through already formed streambeds to eventually reach bedrock and form a placer deposit is very limited in its workability. This theory does not lead a prospector into paying deposits of high-grade gold
Sometimes a storm will have enough force to move large amounts of gold, but will only move a portion of the entire streambed, leaving a lower stratum in place in some locations. When this happens, the gold moving along at the bottom of the flood-layer can become trapped by the irregularities of the unmoving (false bedrock) streambed layer lying underneath. The rocks along the surface of a lower stratum can act as natural gold traps.
Streambed layers caused by different flood storms are referred to as “flood layers.” Flood layers within a streambed are easily distinguished, because they are usually of a different color, consistency and hardness from the other layers of material within the streambed. Sometimes the bottom of a flood layer will contain more gold than is present on bedrock. Sometimes, when more than one flood layer is present in a streambed, there will be more than one layer of flood gold present, too. Gold deposits can often be found in the contact zone between the layers.
Flood layers that are caused by major flood storms are almost always found in a compacted state where the rocks and material hold together tightly and require tools to help pry them apart. In mining, we call this “hard-pack.” There is a big difference between hard-packed streambed and tailings from earlier mining activity or loose streambed material. Almost all high-grade pay-streaks will be found at the bottom of a layer of hard-pack. So it is very important that you know what it is. Please note how hard I have to work to break apart the hard-pack in one of the following 2 video segments:
The larger that a piece of gold is, the faster it will work its way down toward the bottom of a flood layer as it is being washed downstream during a flood. The finest-sized particles of gold might not work their way down through a flooding layer at all, but might remain dispersed up in the material.
So, you can run across a flood layer which has a line of the heavier pieces of gold along its bottom edge, or a flood layer which contains a large amount of fine gold dispersed throughout the entire layer. You can also run across a flood layer which contains a lot of fine gold dispersed throughout, in addition to a line of heavier gold along the bottom edge.
Not all flood layers contain gold in paying quantities for the small-sized mining operation. But in gold country, all flood layers do seem to contain gold in some quantity, even if only microscopic in size.
Some of the best areas to test for paying quantities of flood gold are where the stream or river widens out, or levels out, or changes the direction of its flow. Such places always cause the flow of water in a storm to slow up in certain locations. This can allow concentrations of gold to collect either on bedrock or in the contact zones between layers. These following important videos demonstrate the most common areas where pay-streaks are formed:
Gravel bars, especially the ones located towards the inside of bends, tend to collect gold. Flood gold in bar placers is sometimes consistently distributed throughout the entire gravel bar. Often the lower-end of a gravel bar is not as rich as the head of the bar, but the gold there can be more uniformly distributed throughout the material.
- Here is where you can buy a sample of natural gold.
- Here is where you can buy Gold Prospecting Equipment & Supplies.
- Prospecting for Gold in Hard-packed Streambed
- More about how to prospect for gold
- Schedule of Events
- Books & Videos by this Author